Wenzhou Wujing Fastener Co., Ltd. specializes in providing and exporting precision fasteners for automotive, construction, home appliances, and sanitary industries. With over 10 years of experience, we offer custom solutions that meet the highest standards for performance and material quality.
Products
Reliable Fasteners for Every Industry. Exceptional Quality. Unmatched Expertise.
Multi-process collaboration to create a one-stop metal parts processing solution
In the field of metal parts processing, our factory provides customers with full process solutions from raw materials to finished products with the integration of multiple composite processes. Each process is carefully designed and strictly controlled to ensure high precision, high reliability and high cost performance of the final product. Here are our core processes and their benefits, as well as the combined value of a combination of processes.
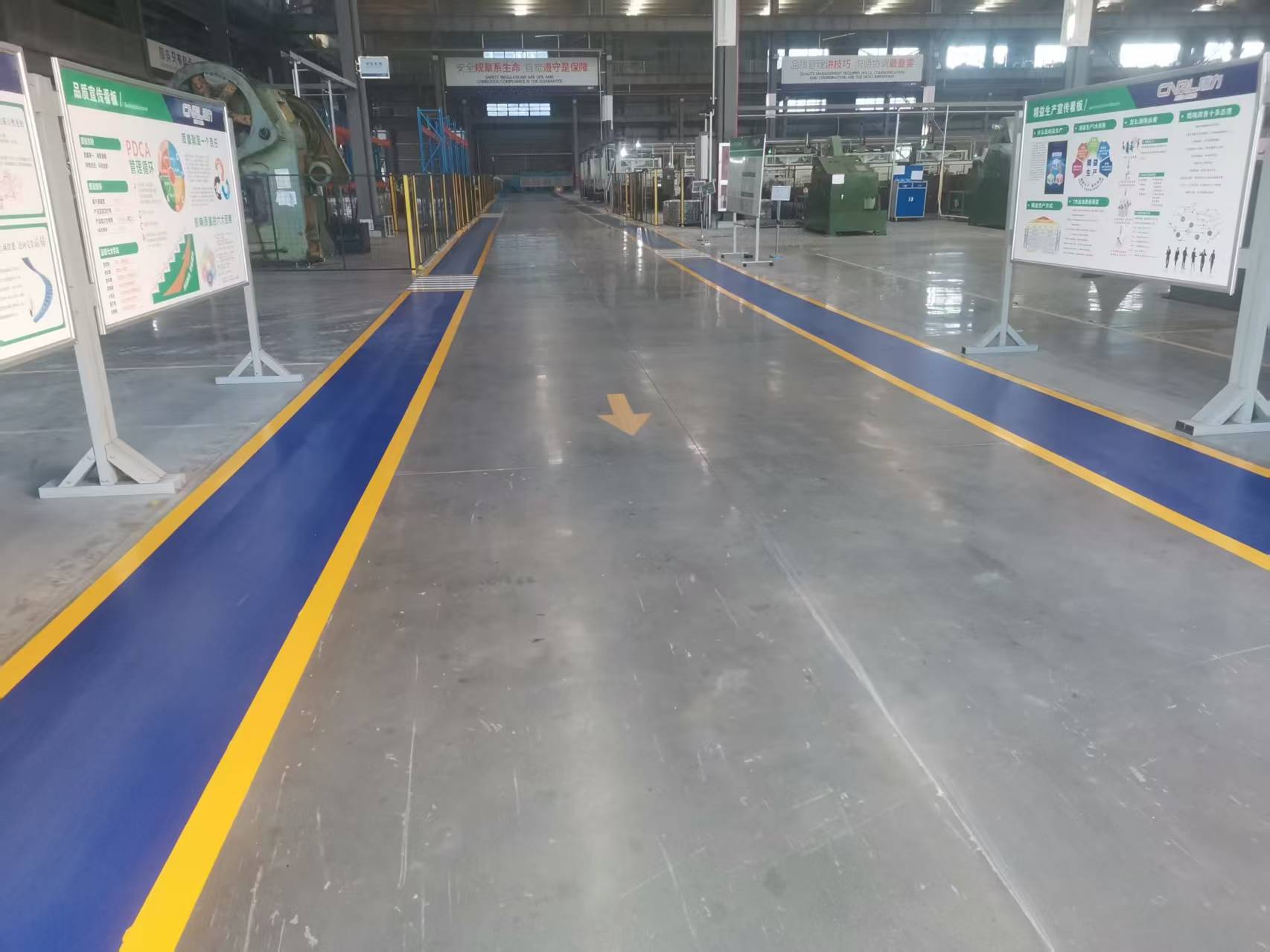
1. Raw Material Drawing: Precision Drawing, Laying the Foundation for Quality!
-
Features: Through the drawing process, the diameter, roundness, and surface quality of wires or rods are precisely controlled, providing high-precision raw materials for subsequent processing.
-
Key Points: Reduces material waste, improves material utilization, and ensures product consistency.
2. Mold Design and Processing: Ingenious Design, Precision Forming!
-
Features: Custom molds are designed according to customer requirements to ensure accurate realization of product shape, size, and functionality.
-
Key Points: Shortens development cycles, reduces mold costs, and improves production efficiency.
3. Cold Heading Processing: Cold Heading Forming, Efficient and Precise!
-
Features: Efficiently produces high-precision, high-strength parts at room temperature, suitable for mass production.
-
Key Points: Saves materials, enhances production efficiency, and improves mechanical properties of parts.
4. Cold Extrusion Processing: Powerful Extrusion, Complex Forming!
-
Features: Uses high pressure to extrude metal materials into shape, suitable for manufacturing complex-shaped parts.
-
Key Points: Improves material utilization, reduces subsequent processing steps, and lowers costs.
5. CNC Machining: CNC Precision Carving, Accurate and Flawless!
-
Features: Achieves high-precision machining of complex-shaped parts through CNC machines, suitable for small-batch customized production.
-
Key Points: High machining accuracy, excellent flexibility, and rapid response to customer needs.
6. Stamping Processing: Rapid Stamping, Efficient Forming!
-
Features: Uses molds and stamping equipment to quickly form thin-walled parts, suitable for mass production.
-
Key Points: High production efficiency, low cost, and ideal for standardized part manufacturing.
7. Grinding Processing: Precision Grinding, Pursuing Excellence!
-
Features: Achieves high-precision dimensional control and surface finish improvement through grinding processes.
-
Key Points: Enhances part accuracy and surface quality, meeting high-demand application scenarios.
8. Thread Processing: Precision Threads, Secure Connections!
-
Features: Processes internal and external threads through rolling or cutting, ensuring thread accuracy and strength.
-
Key Points: Improves part connection performance and meets diverse requirements.
9. Heat Treatment Processing: Heat Treatment Tempering, Strong and Tough!
-
Features: Improves material hardness, strength, and wear resistance through quenching and tempering processes.
-
Key Points: Enhances mechanical properties of parts and extends service life.
10. Induction Hardening: Localized Hardening, Precise Strengthening!
-
Features: Uses induction heating to harden the surface of parts locally, improving surface hardness and wear resistance.
-
Key Points: Energy-efficient, minimal deformation, and suitable for localized strengthening needs.
11. Surface Treatment Processing: Surface Finishing, Elevating Quality!
-
Features: Enhances corrosion resistance, wear resistance, and aesthetics of parts through plating, spraying, oxidation, and other processes.
-
Key Points: Improves environmental adaptability of parts and adds value to products.
Advantages of Multi-Process Collaboration: Multi-Process Synergy, Creating a One-Stop Solution!
Our factory’s core competitiveness lies in seamlessly integrating multiple processes to form an efficient and flexible production system. Below are the comprehensive advantages brought by multi-process collaboration:
-
One-Stop Service: From raw materials to finished products, all processes are completed in-house, reducing intermediate links and ensuring controllable delivery times and quality.
-
Cost Optimization: By rationally designing the processing chain, material waste and processing steps are minimized, offering customers more competitive pricing.
-
Quality Assurance: Strict quality control runs through every process, ensuring high precision and reliability of the final product.
-
Flexible Response: Multi-process collaboration enables the factory to quickly adapt to diverse customer needs, providing customized solutions.
-
Technical Synergy: Seamless integration of processes maximizes the advantages of each process, improving overall production efficiency.
Conclusion:
By integrating multiple advanced processes, we provide customers with a full-range solution from design to finished products. Whether for mass standardized production or small-batch customized needs, we deliver the optimal process combination, strict quality control, and competitive pricing to meet your expectations and help your projects succeed!